Tempco’s Silicone Rubber Heaters
Construction Characteristics
Silicone Rubber Heaters are thin, flexible, electric heaters that can be used up to 500°F/260°C intermittently and 392°F/200°C continuously. They are physically resistant to many adverse operating conditions. They are manufactured with either a rough or smooth material and with either a wire-wound or etched foil heating element. They are ideal for a large variety of applications and industries.
Rough fiberglass/silicone material:
- Rough silicone has a more durable texture
- Standard construction for plain, wire-wound flexible heaters
Smooth fiberglass/silicone material:
- Tends to be more flexible
- Stain-resistant
- Standard construction for heaters with PSA or heaters vulcanized to a metal plate
Flexible silicone rubber heaters can be a simple solution to a complex heating problem. They can be produced using different material thicknesses and textures. Multiple layers can be applied for a thicker heater application. Additional layers can be used to create an outer seal around the internal heater. For example, a two-layer 10″× 10″ heater can be sandwiched between two 11″ × 11″ outer layers.
The internal heat distribution pattern(s) allows for the heater element wire to be placed as close as 5/32″ from the edge of the flexible heater. The heat pattern can be distributed to accommodate holes or cutouts or to concentrate the heat in specific sections of the flexible heater as the application dictates.
Wire-Wound Element Construction
Tempco Silicone Rubber heaters with wire-wound heating elements provide excellent physical strength capable of withstanding repeated flexing without compromising the life and performance of the heater. They are also ideal for use with geometrically challenging shapes, including three-dimensional ones. The wire-wound element process consists of a resistance wire wound on a fiberglass cord for added support and flexibility.
The wire-wound element can be laid out in specially designed patterns that can accommodate a variety of conditions:
- specific heat profiles – designed to be uniform or to concentrate heat in a specific section
- various size and shape heaters
- avoidance of holes or cutouts
Power lead wires or cord sets are attached to the heater windings with solder. They are firmly secured in place through a vulcanizing process, ensuring that the assembly becomes homogenous.
The wire-wound process is recommended and preferred for small to medium size quantities, medium to large size heaters, and to produce prototypes to prove out the design parameters prior to entering into large volume production runs when using etched foil.
Etched Foil Element Construction
Tempco Silicone Rubber Heaters with etched foil heating elements are made with a thin metal foil (.001″), usually a nickel base alloy, as the resistance element. The resistance pattern to be etched is designed in CAD and transferred to the foil, which is laminated to the insulating substrate. The element/substrate is then processed through an acid spray to produce the desired resistance pattern. The top layer is added and vulcanized. Lead wires are then attached to the heater and insulated with additional silicone rubber to complete the heater.
Due to the large, flat surface area, an etched foil heater has exceptional heat transfer properties compared to wire-wound element heaters. It can deliver more uniform heat profiles with higher watt densities, providing longer operating heater life. It can also be zoned with distributed wattage or separate heating circuits to compensate for load variations.
The etched foil process is recommended for small-size heaters in large quantities.
Flexible Heater Wattage Recommendations
Step 1: Determine the Required Wattage
Every process has a unique wattage requirement to heat that particular load up to temperature or to maintain a particular temperature. If the required heater wattage is not known, estimate the required wattage using the thermodynamic formulas. A safety factor of 25% additional wattage is recommended to compensate for unknown variables.
Step 2: Determine the Heater Size and Watt Density
A flexible heater should use the maximum space available for mounting and heating the process. Factors that affect heater size include the mounting method and watt density.
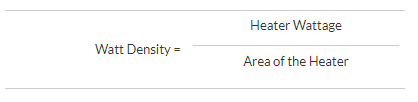
As a general rule, the following can be applied for silicone rubber heaters:
- Low Heat-Up: 2.5 w/in2
- Average Heat-Up: 5 w/in2
- High Heat-Up: 7.5 w/in2 and greater
Design Features
- Excellent performance under adverse conditions
- Low mass construction
- Rapid heat-up
- Custom design
- Temperature range of -70°F to +500°F (-56.6°C to +260°C)
- Wire-wound or etched-foil construction types
- Variety of material thicknesses available
Efficient and Trouble-Free Performance
Tempco’s Flexible Heaters are capable of operating with excellent performance under many adverse conditions, including:
- moisture
- outdoor exposure or ambient temperatures
- radiation
- ozone
- compression set
- vacuum
- fungus
- oils
- solvents and other chemicals
The low thermal mass of flexible heaters allows their use in applications where the space for placing a heater is limited and weight is a concern. Flexible Silicone Rubber have very good mechanical properties. They are of low mass construction and provide rapid heat-up due to direct bonding to the part where applicable — a desired requirement for applications where precise temperature control is important to the overall quality of the application. Flexible Heaters will not stretch or tear within a temperature range of -70°F to +500°F (-56.6°C to +260°C) and are not affected by:
- mechanical shock
- vibration
- repeated flexing
Custom Silicone Rubber Heater Designs
Common Applications
- Common Applications
- Additive Manufacturing
- Aerospace
- Air Horns
- Aircraft Comfort Heaters
- Airplane Propeller Repair
- Animal Feeders
- ATM Machines
- Autoclaves
- Automotive
- Battery Heaters
- Computer Memory Planes
- Copy Machines
- Credit Card Scanners
- De-Icing
- Drum Heaters
- Food Service Equipment
- Graphic Arts Equipment
- Guidance Systems
- Gyroscopes
- Heated Presses
- Incubators
- Laboratory Equipment
- Laminators
- Liquid Reservoirs
- Medical Equipment
- Mirror Heaters
- Optical Equipment
- Outdoor Antennas
- Packaging Machinery
- Photo Processing
- Recovery Systems
- Refrigeration Equipment
- Security Equipment
- Semiconductor Equipment
- Shoe Machinery
- Turbine Propeller Repair
- Vacuum Chamber
- Vending Machines
- X-Ray Processing